Il mondo della tecnologia cresce a vista d’occhio ed il settore della robotica non fa eccezione. Al giorno d’oggi, negli ambienti lavorativi sempre di più si ha la necessità di introdurre dei robot che possano aiutare gli operatori.
Robot mobili: cosa sono
I robot mobili sono dei dispositivi intelligenti che hanno la capacità di spostarsi in completa autonomia all’interno di spazi limitati, riuscendo ad eseguire alcune attività che, normalmente, spetterebbero ad un operatore umano, come l’evasione di ordini o il trasporto di merci.
L’autonomia di spostamento è dovuta all’installazione di sensori, software di mappatura digitale e di intelligenza artificiale, che permettono al robot non solo di fargli conoscere la sua posizione nello spazio, ma anche le prossime azioni da compiere e i percorsi che deve seguire.
I robot mobili, anche detti Autonomous Mobile Robots (AMR), hanno la capacità di connettersi in modalità wireless con gli altri sistemi che si trovano all’interno della fabbrica: ciò permette che si possano interfacciare con le macchine già presenti. Inoltre queste connessioni verranno ulteriormente potenziate grazie all’introduzione della tecnologia 5G.
Esistono vari tipi di AMR, per esempio:
- Robot per il picking: A seconda della logica di prelievo, ne esistono due sottogruppi:
- AMR per prelievo “uomo alla merce”: Robot che accompagna l’operatore, il quale è incaricato di prelevare i prodotti dagli scaffali e depositarli nel robot stesso. Una volta fatto questo, il robot si occupa di trasferirli nell’area di confezionamento.
- AMR per prelievo “merci all’uomo”: Robot in grado di sollevare l’intero scaffale su cui il prodotto si trova e spostarlo in una posizione di picking, permettendo al magazziniere di procedere con gli ordini.
- Robot per catalogo e smistamento articoli: Questi robot si occupano della classificazione dei prodotti, grazie ad un vassoio reclinabile e un lettore di codici che permette loro di ordinare i pacchetti e sistemarli nella posizione corretta.
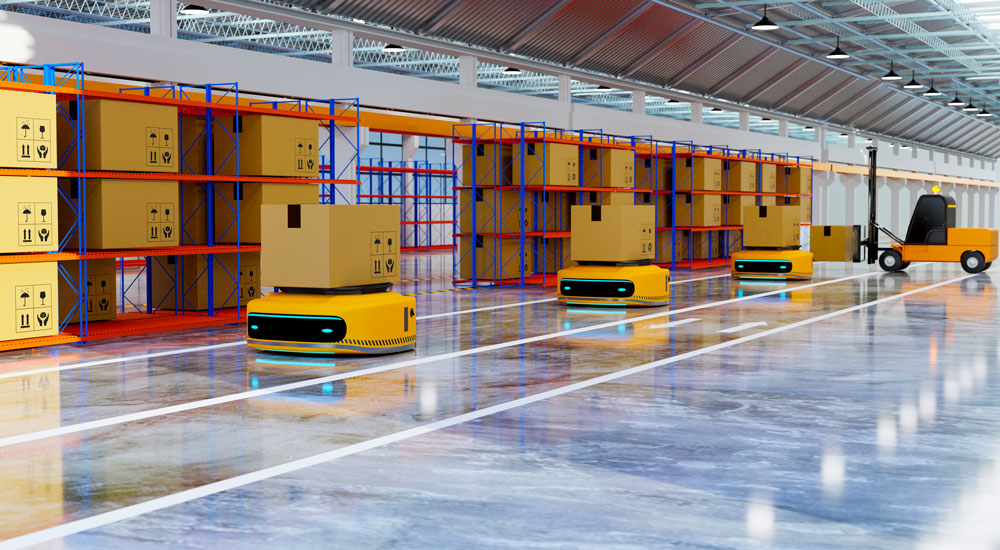
Robot autonomi: la tecnologia alla loro base
A differenza di altri dispositivi, gli Autonomous Mobile Robots non hanno alcun bisogno di cavi esterni o particolari sensori per muoversi nello spazio, fanno affidamento al loro sistema di mappatura di bordo, software che definisce il tragitto di un robot man mano che si sposta tra un punto e l’altro del magazzino. Come risultato, gli AMR riescono ad essere autonomi grazie alle informazioni che ricevono durante il tragitto, permettendo in tempo reale di cambiare rotta se in presenza di ostacoli, o persone.
In particolar modo per l’operatore umano, questo rappresenta un aspetto molto importante dal punto di vista della sicurezza. Infatti, gli AMR sono dispositivi che sono stati progettati appositamente per collaborare con l’essere umano. Come conseguenza, gli AMR sono chiamati al rispetto delle linee guida sulla sicurezza dei prodotti destinati ai robot avanzati, in aggiunta alla normativa UNI EN 1525-1999, riguardante i carrelli industriali.
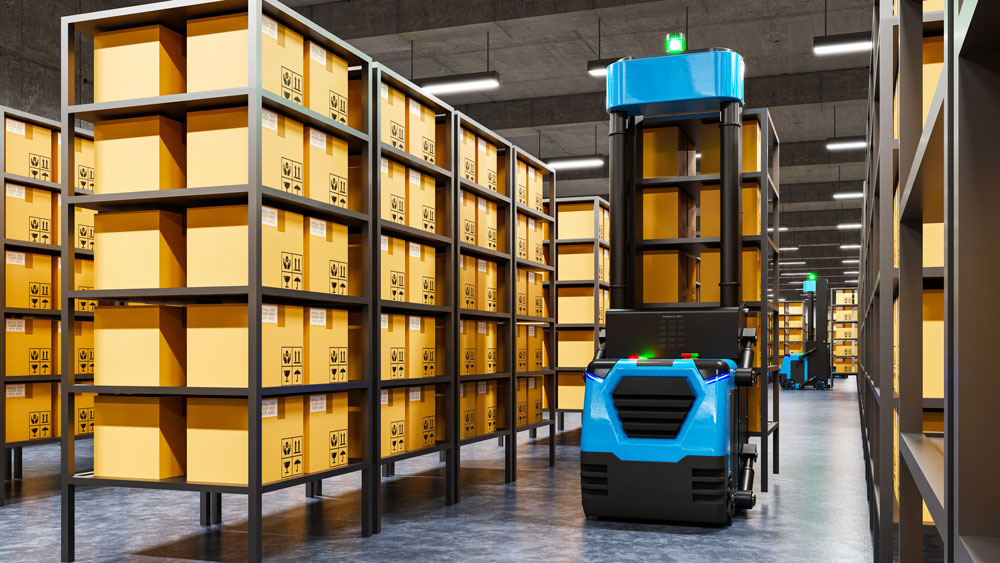
Le differenze tra Autonomous Mobile Robots (AMR) e Automated Guided Vehicles (AGV)
Prima dell’introduzione dei robot autonomi, nelle fabbriche erano ampiamente utilizzati altri dispositivi, ossia gli Automated Guided Vehicles (AGV). Se i primi costituiscono dei sistemi in grado di prendere delle decisioni in autonomia grazie ad una tecnologia a bordo molto sofisticata, i secondi sono dei dispositivi più semplici che obbediscono solamente ad una serie di istruzioni.
Gli AVG sono in grado di muoversi solamente lungo un tragitto predefinito, affidando la loro capacità di spostamento a cavi, sensori e bande magnetiche. Inoltre, se gli AMR sono in grado di rilevare un ostacolo, un AVG rimane in attesa che ciò che ha davanti venga rimosso dal suo percorso. Per quanto riguarda la merce che viene trasportata, un AMR è in grado di trasportare delle unità leggere, differentemente da un AVG, destinato prevalentemente alla movimentazione di pallet.
Un’altra rimarcabile differenza riguarda la gestione di questi dispositivi: un AMR è manovrabile tramite l’interfaccia o il software che gestisce la flotta di più robot contemporaneamente che collaborano tra loro. La flessiblità degli Autonomous Mobile Robots li rende perfetti ad essere impiegati nelle linee di produzione dove ci sono modifiche quotidiane.
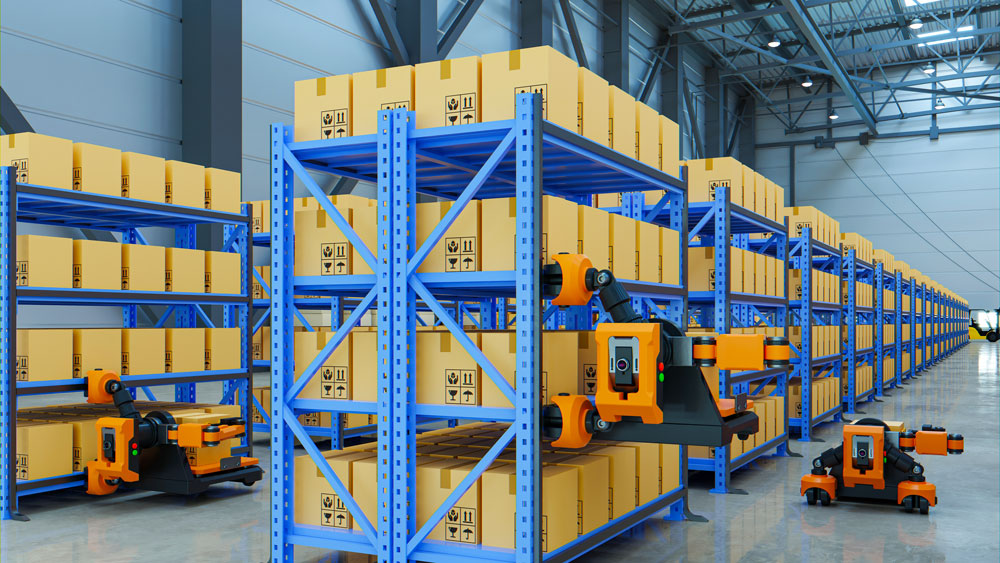
Robot mobili autonomi: applicazioni nell’industria 4.0
Le caratteristiche che fornisce un Autonomous Mobile Robots si sposano perfettamente coi principi dell’industria 4.0. I robot autonomi sono facilmente implementabili in tutti quei settori che necessitano movimentazione interna: Per esempio, si va dall’industria dell’automotive a quella della logistica, nel reparto produzione allo stoccaggio in magazzino.
Proprio per quanto riguarda il settore logistico, con la proliferazione delle piattaforme di e-commerce, gli AMB verranno sempre più usufruiti all’interno di nuovi hub logistici. In conclusione, nonostante i robot mobili siano gia utilizzati, nel futuro potremmo avere la possibilità di averne sempre più multitasking, con tassi di affidabilità e flessibilità particolarmente elevati.
Leggi anche l’articolo: Model Based Systems Engineering: caratteristiche, vantaggi e applicazioni